My experience with Aircraft Parts distribution started back in 2007 when, after almost a decade in IT and Data Warehousing, I was hired to run Operations for an Aircraft Parts broker. One of the first documents I encountered on the job was the Quality Manual. Later on, I learned that this rather lengthy document was part of the Quality Management System (QMS), the collection of processes, policies, procedures, resources, assets, and cultural values aimed at helping an organization continuously improve and achieve its goals of customer satisfaction and organizational efficiency. The Quality Manual quickly became my go-to for all “when in doubt” situations.
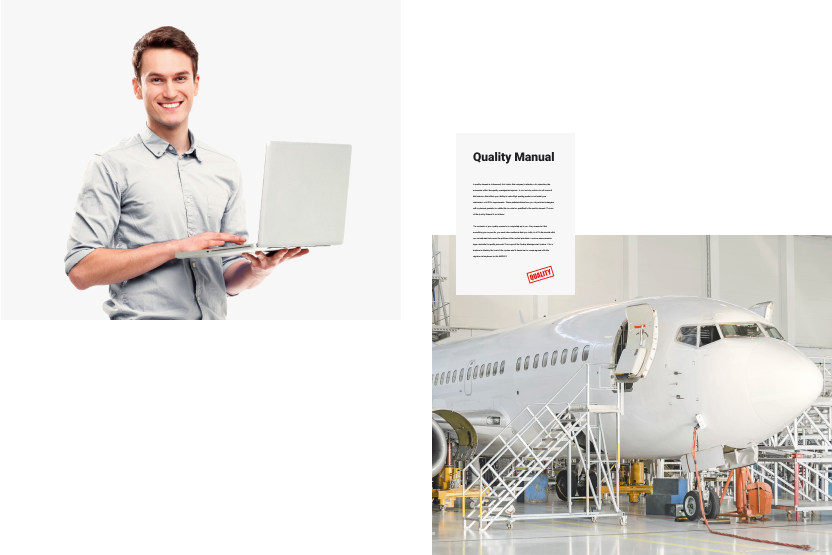
The major international standard we often refer to when talking about QMS is ISO 9000. Since its inception in 1987, it’s been widely accepted by millions of organizations across the world. The ISO 9000 family of standards has gained popularity because it offers a framework for improving quality without dictating what an organization’s objectives should be or prescribing precisely how to achieve them. It offers a standardized vocabulary to bridge understanding and gives fundamental guidance that’s applicable to any organization looking to provide products and services that consistently meet the requirements and expectations of customers in the most efficient manner possible.
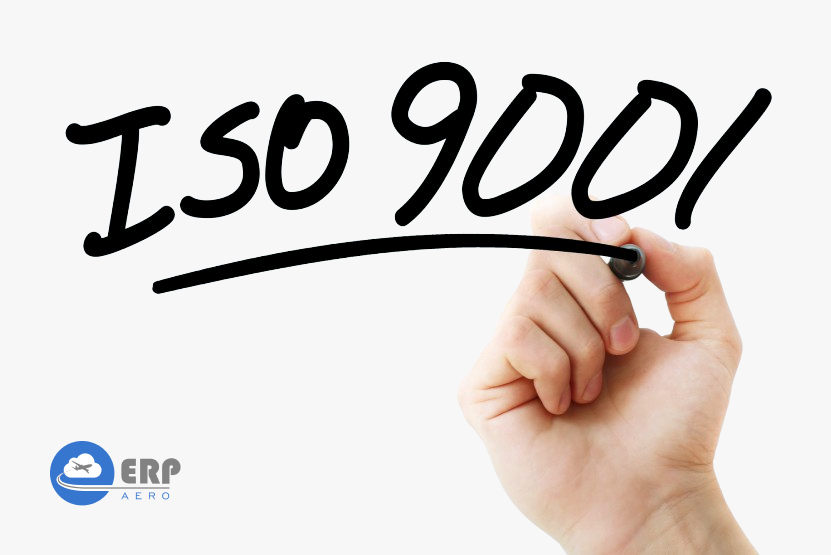
The Federal Aviation Administration (FAA) itself is certified to ISO 9001 and the FAA Advisory Circular 00-56 lists ISO 9001 as an acceptable quality standard for FAA 145 MROs and FAA 00-56B distributors. Soon after the acceptance of ISO 9001 by the FAA, the Aviation Suppliers Association (ASA) became an accredited certification body for ISO 9001.
In 2015, a new version of ISO 9001 was published in response to the growing global supply chain size and complexity and the exponential increase in the availability of technology, products, and services for consumers. New requirements were needed to keep pace with the rapid growth and to support companies in meeting ever-greater expectations.
Implementation of the new ISO 9001:2015 standard meant a re-familiarization with the terms we learned in business school: Leadership, Performance Evaluation, Continual Improvement, Reporting, SWAT Analysis, and… Risk-Based Thinking.
While Quality Control and Sales bemoaned the inconvenience of transitioning to the new standard, we were busy applying a risk-based approach to imagine every “what-if” scenario possible and use our findings to uncover blind spots and identify areas for improvement.
Paper documents & closed offices
One of the obvious shortcomings we found was our heavy reliance on paper documents and the inability of our ERP system at the time to easily store, manage, and retrieve documents upon request. Our risk-based analysis also revealed that we had no system built into our aerospace ERP for ranking customers or tracking supplier ISO/ASA credentials and other information that could help immensely in making decisions on whether or not to add a supplier to our Approved Suppliers List (ASL).
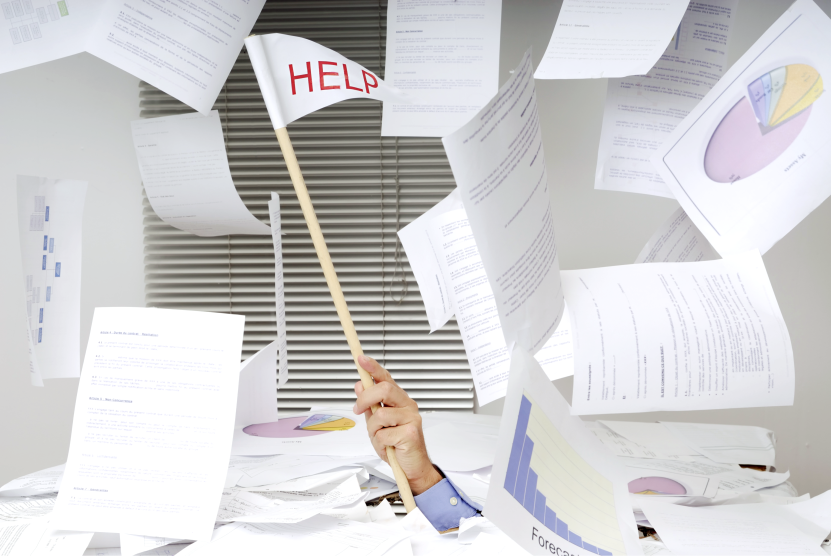
Thinking back on our “what-if” exercise, I remember discussing a scenario that, at the time, most thought unlikely (if not impossible). It was this: “What if the offices of our company or the offices of our suppliers aren’t able to open for business? What impact would that have?” Today, after the events of 2020, this may sound painfully familiar… not impossible after all. It was this specific “what-if” that led us to recognize the potential risks of relying so heavily on our physical office and warehouse space. This helped us envision what was needed in order to run operations remotely.
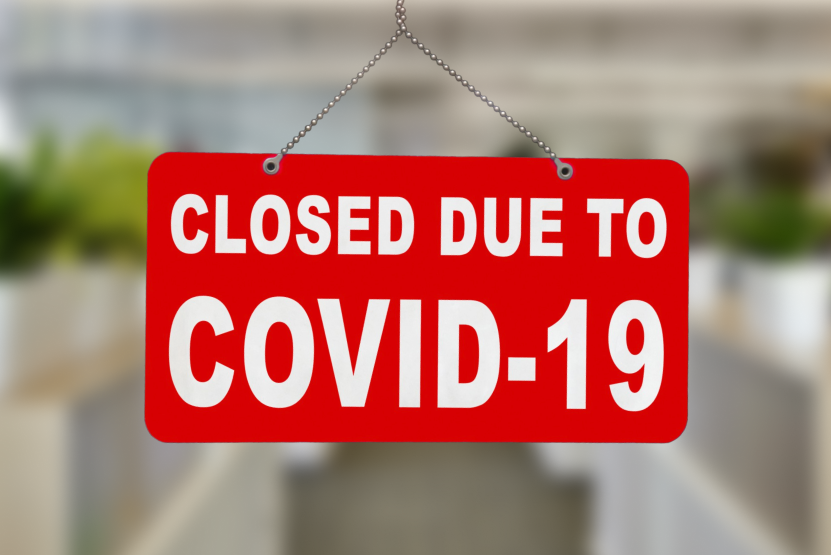
It became evident that the two ERP systems we were using at the time to conduct business were inadequate. Our situation was made further challenging when we learned that the other ERP solutions that were widely accepted by and dominant in our industry were also lacking. No platform existed to meet the new quality standards or address the potential risks we had identified. So, we decided to create a new ERP platform that would provide a paper-less solution, allow companies in the space to move away from office/warehouse centricity, fulfill the ISO 9001 and ASA-100 quality standards, and capitalize on Customer Relationship Management (CRM) capabilities to inform Risk Assessment in business transactions.
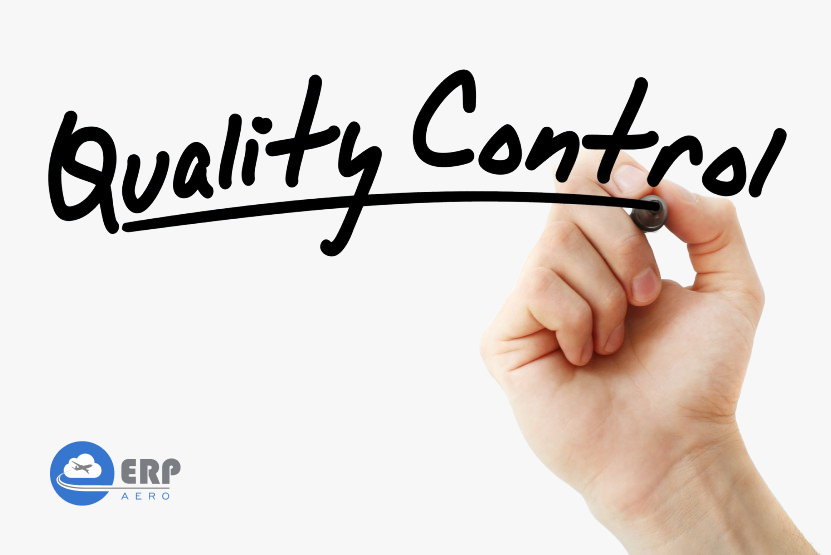
Fast-forward four years:
- Year 2019 – our pilot customer passes ISO 9001:2015 and FAA 00-56B Certification with a paper-less ERP solution that includes automatically-generated ASL and Equipment Calibration reports along with a fully Electronic Document Management System (EDMS) with transaction traceability.
- Year 2020 – after switching from another ERP in December 2019, our customer in Italy does not lose a single day of operation, successfully achieves ISO Certification, and expands business with the opening of a Middle-East Subsidiary.
- Year 2020 – our customer in Switzerland successfully achieves ASA-100 Certification.
- Year 2020 – our US-based customer successfully passes ASA-100 Certification with high regards from inspector for their ability to retain and quickly produce trace documentation.
I will conclude my article with a recent message I received from the President of our pilot customer: “In 2020, we decided to move from California to Florida to optimize our costs and lead-times for European Airlines. During the Audit by ASACB, the inspector regarded our ability to move physical offices and retrieve and present corporate data remotely, without the need to ever go on-site to recover documentation. Thank you.”